難點主要有以下幾個方面:
1、切削力大,機械零件加工切削溫度高;該類型材料強度大,切削時切向應力大、塑性變形大,因而切削力大。此外材料導熱性極差,造成切削溫度升高,且高溫往往集中在刀具刃口附近的狹長區(qū)域內,從而加快了刀具的磨損。
2、不銹鋼零件加工硬化嚴重--奧氏體不銹鋼以及一些高溫合金不銹鋼均為奧氏體組織,切削時加工硬化傾向大,通常是普通碳素鋼的數(shù)倍,刀具在加工硬化區(qū)域內切削,使刀具壽命縮短。
3、不銹鋼零件加工容易粘刀--無論是奧氏體不銹鋼還是馬氏體不銹鋼均存在加工時切屑強韌、切削溫度很高的特點。東莞機械零件加工當強韌的切屑流經前刀面時,將產生粘結、熔焊等粘刀現(xiàn)象,影響加工零件表面粗糙度。;
4.不銹鋼零件加工刀具磨損加快--上述材料一般含高熔點元素、塑性大,切削溫度高,數(shù)控機床加工使刀具磨損加快,磨刀、換刀頻繁,從而影響了生產效率,提高了刀具使用成本。
加工方法的選擇與加工方案的確定
(一)加工方法的選擇
加工方法的選擇原則是保證加工表面的加工精度和表面粗糙度的要求。東莞精密電腦鑼加工由于獲得同一級精度及表面粗糙度的加工方法一般有許多,因而在實際選擇時,要結合零件的形狀、尺寸大小和熱處理要求等全面考慮。例如,對于IT7級精度的孔采用鏜削、鉸削、磨削等加工方法均可達到精度要求,但箱體上的孔一般采用鏜削或鉸削,而不宜采用磨削。一般小尺寸的箱體孔選擇鉸孔,當孔徑較大時則應選擇鏜孔。此外,還應考慮生產率和經濟性的要求,以及工廠的生產設備等實際情況。常用加工方法的經濟加工精度及表面粗糙度可查閱有關工藝手冊。
(二)加工方案確定的原則
零件上比較精密表面的加工,常常是通過粗加工、半精加工和精加工逐步達到的。對這些表面僅僅根據(jù)質量要求選擇相應的最終加工方法是不夠的,還應正確地確定從毛坯到最終成形的加工方案。
確定加工方案時,首先應根據(jù)主要表面的精度和表面粗糙度的要求,初步確定為達到這些要求所需要的加工方法。例如,對于孔徑不大的IT7級精度的孔,最終加工方法取精鉸時,則精鉸孔前通常要經過鉆孔、擴孔和粗鉸孔等加工。
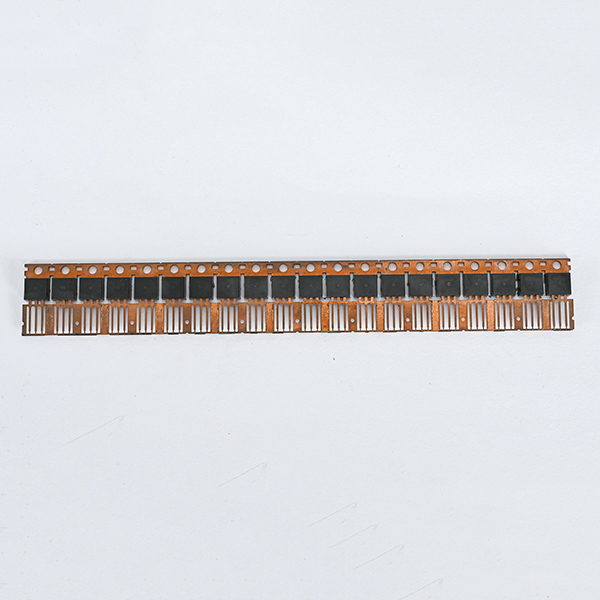